Стандартная экструзионная линия
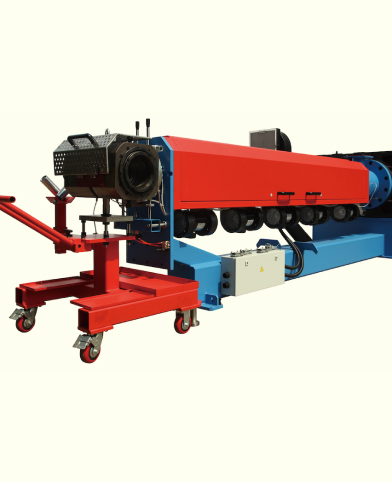
В основном используется для экструзии изоляции/оболочки PVC, PE, PP, XLPE, HFFR, PUR, TPU, PV или безгалогенных материалов.
Технологический процесс экструдирования позволяет совмещать несколько операций изготовления кабельной продукции в одну последовательную цепочку. Поточные линии позволяют повысить производительность за счёт исключения ряда промежуточных операций, экономии производственных площадей и сокращения штата обслуживающего персонала. К тому же открываются возможности для более широкой и комплексной автоматизации производства.
Основными составными частями экструдера являются экструзионная система, трансмиссионная система и система нагрева и охлаждения.
Гранулы пластика через загрузочный бункер опускаются и под действием сил трения между вращающимся шнеком и внутренней стенкой загрузочного бункера измельчаются и подаются вперёд на участок подачи сырья, при этом рыхлые твёрдые частицы вместе с продвижением вперёд уплотняются; на участке сжатия шнековый лото становиться менее глубоким, постепенно увеличивая давление, в то же самое время происходит разогрев цилиндра снаружи и материал, находящийся под воздействием силы трения между шнеком и внутренней стенкой цилиндра, плавится, проходя через участок сжатия; на участке гомогенизации происходит гомогенизация материала, после которой происходит дозированная экструзия материала с определённой температурой под определённым давлением. В передней части экструдера происходит покрытие расплавом поверхности металлического проводника, который проходя через формовку создаёт конечный продукт.
- Стойка
- Замок с фиксаторами
- Электродвигатель
- Нагреватель цилиндра
- Кожух
- Цилиндр
- Шнек
- Основание бункера загрузки
- Ременной шкив редуктора
- Защитный кожух ременного шкива
- Ось толкателя
- Неподвижное основание
- Зубчатый редуктор
- Бункер загрузки сырья
Управление при помощи PLC с сенсорным экраном. Система управления состоит из двух шкафов, в которых помещены все приборы управления экструдеров.
Напряжение питания 3х380 V±5%, 50 Hz, 180 kW;
Охлаждающая вода с температурой 10–15 °C, 1,5 m3/h;
Сжатый воздух 6 bar–2 m3/h.
Экструдерная линия нормально работает при следующих условиях:
Температура окружающей среды от +10 до +30 градусов по Цельсию.
Влажность, максимальная 80% при 30 градусов по Цельсию.
Высота над уровнем моря, максимальная 1000 м.
Среда – взрывобезопасная, без проводящей пыли или агрессивных газов в концентрациях, разрушающих металлических и изоляционных поверхностей.
Двигатель: Siemens, Германия;
Частотный преобразователь: Siemens, Германия;
PLC: Siemens, Германия;
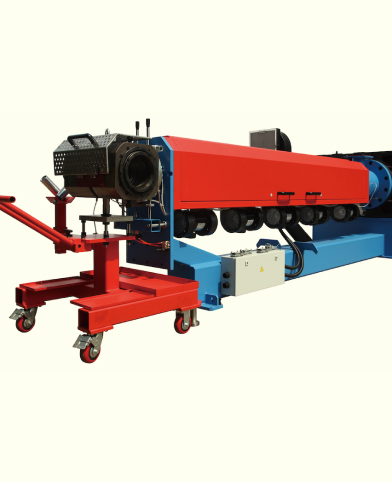
В основном используется для экструзии изоляции/оболочки PVC, PE, PP, XLPE, HFFR, PUR, TPU, PV или безгалогенных материалов.
Технологический процесс экструдирования позволяет совмещать несколько операций изготовления кабельной продукции в одну последовательную цепочку. Поточные линии позволяют повысить производительность за счёт исключения ряда промежуточных операций, экономии производственных площадей и сокращения штата обслуживающего персонала. К тому же открываются возможности для более широкой и комплексной автоматизации производства.
Основными составными частями экструдера являются экструзионная система, трансмиссионная система и система нагрева и охлаждения.
Гранулы пластика через загрузочный бункер опускаются и под действием сил трения между вращающимся шнеком и внутренней стенкой загрузочного бункера измельчаются и подаются вперёд на участок подачи сырья, при этом рыхлые твёрдые частицы вместе с продвижением вперёд уплотняются; на участке сжатия шнековый лото становиться менее глубоким, постепенно увеличивая давление, в то же самое время происходит разогрев цилиндра снаружи и материал, находящийся под воздействием силы трения между шнеком и внутренней стенкой цилиндра, плавится, проходя через участок сжатия; на участке гомогенизации происходит гомогенизация материала, после которой происходит дозированная экструзия материала с определённой температурой под определённым давлением. В передней части экструдера происходит покрытие расплавом поверхности металлического проводника, который проходя через формовку создаёт конечный продукт.
- Стойка
- Замок с фиксаторами
- Электродвигатель
- Нагреватель цилиндра
- Кожух
- Цилиндр
- Шнек
- Основание бункера загрузки
- Ременной шкив редуктора
- Защитный кожух ременного шкива
- Ось толкателя
- Неподвижное основание
- Зубчатый редуктор
- Бункер загрузки сырья
Управление при помощи PLC с сенсорным экраном. Система управления состоит из двух шкафов, в которых помещены все приборы управления экструдеров.
Напряжение питания 3х380 V±5%, 50 Hz, 180 kW;
Охлаждающая вода с температурой 10–15 °C, 1,5 m3/h;
Сжатый воздух 6 bar–2 m3/h.
Экструдерная линия нормально работает при следующих условиях:
Температура окружающей среды от +10 до +30 градусов по Цельсию.
Влажность, максимальная 80% при 30 градусов по Цельсию.
Высота над уровнем моря, максимальная 1000 м.
Среда – взрывобезопасная, без проводящей пыли или агрессивных газов в концентрациях, разрушающих металлических и изоляционных поверхностей.
Двигатель: Siemens, Германия;
Частотный преобразователь: Siemens, Германия;
PLC: Siemens, Германия;
Назначение
В основном используется для экструзии изоляции/оболочки PVC, PE, PP, XLPE, HFFR, PUR, TPU, PV или безгалогенных материалов.
Технологический процесс экструдирования позволяет совмещать несколько операций изготовления кабельной продукции в одну последовательную цепочку. Поточные линии позволяют повысить производительность за счёт исключения ряда промежуточных операций, экономии производственных площадей и сокращения штата обслуживающего персонала. К тому же открываются возможности для более широкой и комплексной автоматизации производства.
Основные системы экструдера
Основными составными частями экструдера являются экструзионная система, трансмиссионная система и система нагрева и охлаждения.
Принцип работы экструдера
Гранулы пластика через загрузочный бункер опускаются и под действием сил трения между вращающимся шнеком и внутренней стенкой загрузочного бункера измельчаются и подаются вперёд на участок подачи сырья, при этом рыхлые твёрдые частицы вместе с продвижением вперёд уплотняются; на участке сжатия шнековый лото становиться менее глубоким, постепенно увеличивая давление, в то же самое время происходит разогрев цилиндра снаружи и материал, находящийся под воздействием силы трения между шнеком и внутренней стенкой цилиндра, плавится, проходя через участок сжатия; на участке гомогенизации происходит гомогенизация материала, после которой происходит дозированная экструзия материала с определённой температурой под определённым давлением. В передней части экструдера происходит покрытие расплавом поверхности металлического проводника, который проходя через формовку создаёт конечный продукт.
Конструкция экструдера
- Стойка
- Замок с фиксаторами
- Электродвигатель
- Нагреватель цилиндра
- Кожух
- Цилиндр
- Шнек
- Основание бункера загрузки
- Ременной шкив редуктора
- Защитный кожух ременного шкива
- Ось толкателя
- Неподвижное основание
- Зубчатый редуктор
- Бункер загрузки сырья
Управление
Управление при помощи PLC с сенсорным экраном. Система управления состоит из двух шкафов, в которых помещены все приборы управления экструдеров.
Питание
Напряжение питания 3х380 V±5%, 50 Hz, 180 kW;
Охлаждающая вода с температурой 10–15 °C, 1,5 m3/h;
Сжатый воздух 6 bar–2 m3/h.
Условия работы
Экструдерная линия нормально работает при следующих условиях:
Температура окружающей среды от +10 до +30 градусов по Цельсию.
Влажность, максимальная 80% при 30 градусов по Цельсию.
Высота над уровнем моря, максимальная 1000 м.
Среда – взрывобезопасная, без проводящей пыли или агрессивных газов в концентрациях, разрушающих металлических и изоляционных поверхностей.
Бренды комплектующих
Двигатель: Siemens, Германия;
Частотный преобразователь: Siemens, Германия;
PLC: Siemens, Германия;

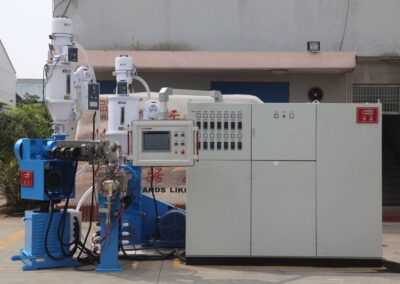
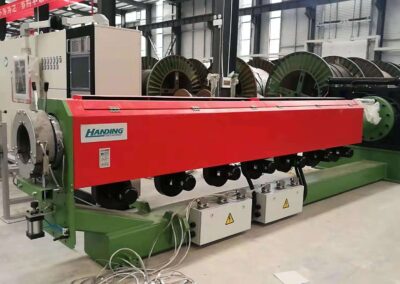
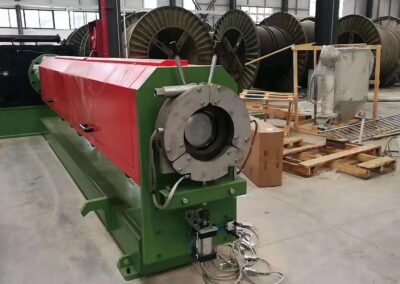
Наименование | Диаметр шнека, мм | Отношение длинны к диаметру | Производительность экструдера, кг/ч | Мощность основного двигателя, кВт | Диаметр кабеля на выходе, мм |
EXT-70x26D | Ø70 | 25:1 | 180 | 37 | 5-25 |
EXT-75x26D | Ø75 | 25:1 | 200 | 55 | 5-30 |
EXT-80x26D | Ø’80 | 25:1 | 250 | 75 | 16-35 |
EXT-90x26D | Ø90 | 25:1 | 350 | 75 | 16-50 |
EXT-100x26D | Ø100 | 25:1 | 450 | 132 | 20-80 |
EXT-120x26D | Ø120 | 25:1 | 550 | 132 | 30-80 |
EXT-150x26DA | Ø150 | 25:1 | 650 | 160 | 50-140 |
EXT-180x26DA | Ø180 | 25:1 | 900 | 185 | 50-140 |
EXT-200x26DA | Ø200 | 25:1 | 1000 | 200 | 35-200 |
Свяжитесь с нами для индивидуального решения
Мы готовы воплотить ваши идеи в реальность. Заполните форму ниже, и наши специалисты свяжутся с вами в ближайшее время для обсуждения всех деталей.